Operational excellence: a winning strategy for companies
Operational excellence is a key concept for modern companies wishing to optimize their performance, improve their competitiveness and meet their customers' requirements. More than a simple objective, it represents a true organizational culture that aims to optimize all internal processes, maximize efficiency and create value at every stage of the production chain.
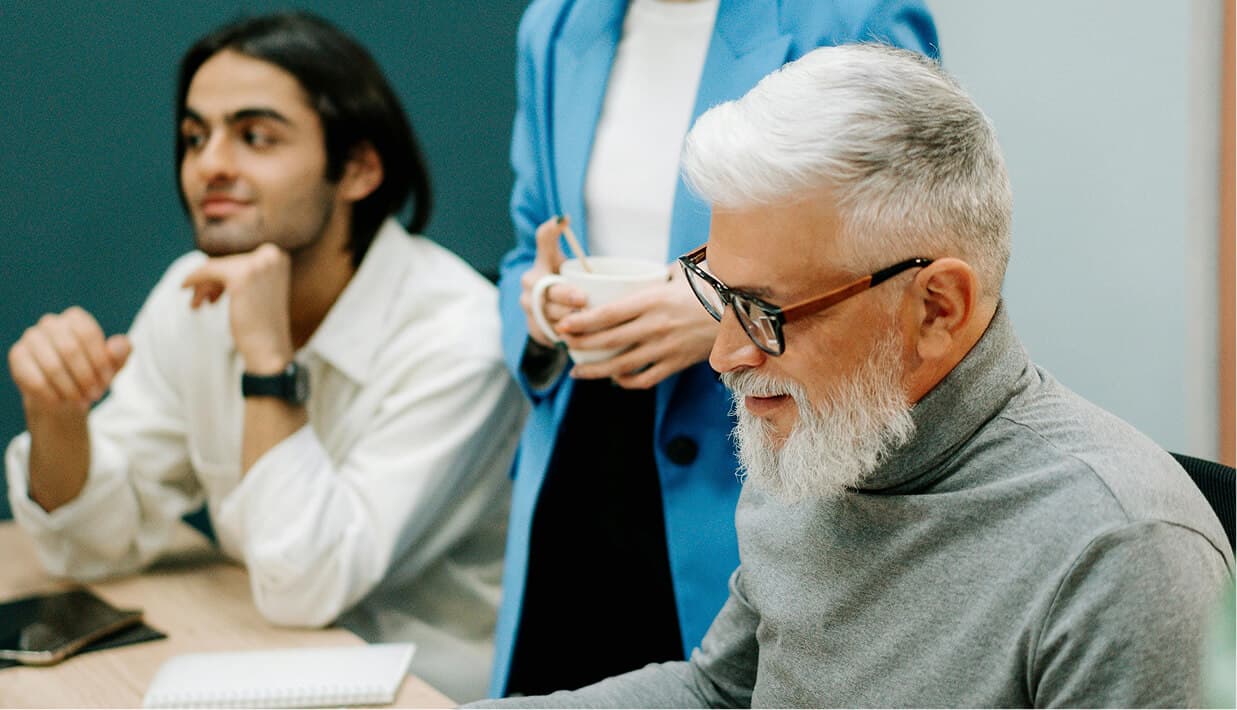
What is Operational Excellence?
Operational excellence designates an organization's ability to deploy optimized processes and permanently improve the quality of its products or services while reducing costs and maximizing customer satisfaction. It's a strategic approach based on continuous improvement, process standardization and innovation in work methods.
Principles of Operational Excellence
Continuous improvement (Kaizen): The idea is to seek constant improvements through simple but regular actions. This involves participation of all company levels, from management to operators.
Quality management: Ensure product or service compliance with defined quality standards throughout the production process.
Waste reduction: Inspired by the Lean method, operational excellence seeks to identify and eliminate waste, whether in terms of time, resources or unnecessary efforts.
Team autonomy: Each employee is encouraged to propose improvements and make decisions to optimize their own work processes.
Performance measurement and analysis: Operational excellence is based on precise performance indicators to measure results, identify friction points and provide effective solutions.
Why is Operational Excellence Crucial?
Profitability improvement: By optimizing processes, a company reduces its costs, improves productivity and maximizes its profit margins.
Increased customer satisfaction: Implementing more efficient processes allows delivering better quality products or services, on time and according to customer expectations.
Adaptability and agility: An organization that adopts operational excellence is more agile in the face of market changes. It can quickly adjust its processes to respond to new requirements or opportunities.
Competitive advantage: By continuously improving its processes, a company becomes more competitive and better positioned to face competition in its market.
Employee motivation: Employees involved in continuous improvement and process optimization feel valued and more engaged.
How to Implement Operational Excellence?
1. Identify Key Objectives: Before starting any operational excellence initiative, it's essential to define clear objectives. Whether reducing costs, improving quality or increasing customer satisfaction, each action must be aligned with the company's global strategy.
2. Map Processes: Once objectives are defined, the next step consists of mapping existing processes. This allows identifying friction points, waste and improvement areas. This diagnostic step is crucial for knowing where to start.
3. Involve all employees: Operational excellence cannot be imposed top-down. It's essential that each employee, at all levels, be involved in the approach. Training, brainstorming meetings and regular exchanges will create a collaborative environment conducive to innovation.
4. Implement improvement methods: Among the most used methods to achieve operational excellence, we find Lean Management (an approach focusing on waste elimination), Six Sigma method (a rigorous framework aimed at reducing defects) and Visual Management (use of control dashboards and visual indicators).
5. Monitoring and adjustments: Once improvements are implemented, it's crucial to regularly monitor obtained results. Thanks to measurement tools and performance indicators, you can adjust strategies and maintain continuous improvement dynamics.
Key Tools for Operational Excellence
To achieve operational excellence, several tools and methodologies can be used, including:
KPI Dashboards: These key performance indicators allow tracking progress made in real time.
Production management software: These tools help better plan, execute and optimize production processes.
Quality management tools: To ensure product compliance with expected standards and norms.
SWOT Matrix: A strategic tool to identify strengths, weaknesses, opportunities and threats related to internal processes.
Conclusion: Operational Excellence, a Lasting Advantage for Your Company
Operational excellence is more than a simple improvement method: it embodies a true business culture that aims to optimize every aspect of the organization. By adopting this approach, companies can not only improve their profitability and competitiveness, but also offer constant added value to their customers.
By implementing an operational excellence strategy, you provide yourself with the means to succeed in an increasingly demanding and dynamic economic environment. Don't wait any longer to make operational excellence a lever of lasting success for your company!
Descubra nossas soluções industriais
Quote Request
Fill out this form to receive a personalized quote for your specific needs. Our sales team will contact you within 24 business hours.
The collected information is subject to computer processing intended to simplify the relationship between the contact form sender and MaKitLeancompany. The recipients of the data are the design department and the sales department of the company. In accordance with the General Data Protection Regulation (GDPR), you have the right to access and rectify information concerning you, which you can exercise by contacting the sales department.
You can also, for legitimate reasons, object to the processing of data concerning you by contacting us through form, phone or email.
For more information, consult our legal terms.