Operational Performance: Optimize processes to maximize efficiency
In an increasingly competitive economic environment, improving operational performance is essential for any company wishing to remain agile, profitable and efficient. Operational performance designates an organization's ability to optimize its internal processes in order to provide products or services faster, more efficiently and more profitably, while meeting customer expectations.
What is Operational Performance?
Operational performance refers to the effectiveness and efficiency of an organization's internal processes. It measures the extent to which a company's operations contribute to value creation while minimizing costs, reducing lead times and maximizing quality.
To achieve optimal operational performance, a company must focus on several key factors: process management, resource management and alignment with strategic objectives. High operational performance allows an organization to produce faster, reduce its costs and improve customer satisfaction.
Key Performance Factors
Simplify your component organization with our Kitting solutions
Benefits of Operational Performance
Cost reduction: By eliminating waste and improving efficiency, companies can reduce their operational costs.
Quality improvement: Optimized processes lead to better product or service quality, thus increasing customer satisfaction.
Competitive advantage: Increased performance allows a company to respond faster to market demands and adapt to changes.
Increased profitability: Process optimization allows generating more revenue with fewer resources.
Employee satisfaction: More efficient processes and improved work environment contribute to better employee satisfaction.
Conclusion: The Importance of Operational Performance
Operational performance is essential for any company seeking to maximize its efficiency, reduce its costs and increase its profitability. By optimizing internal processes, implementing rigorous quality management and investing in automation and modern technologies, companies can gain significant competitive advantage.
By implementing methodologies like Lean, Six Sigma or Kaizen, and by regularly measuring performance with the help of key indicators, an organization can continuously improve its performance, create more value for its customers and strengthen its market position.
Découvrez nos solutions industrielles
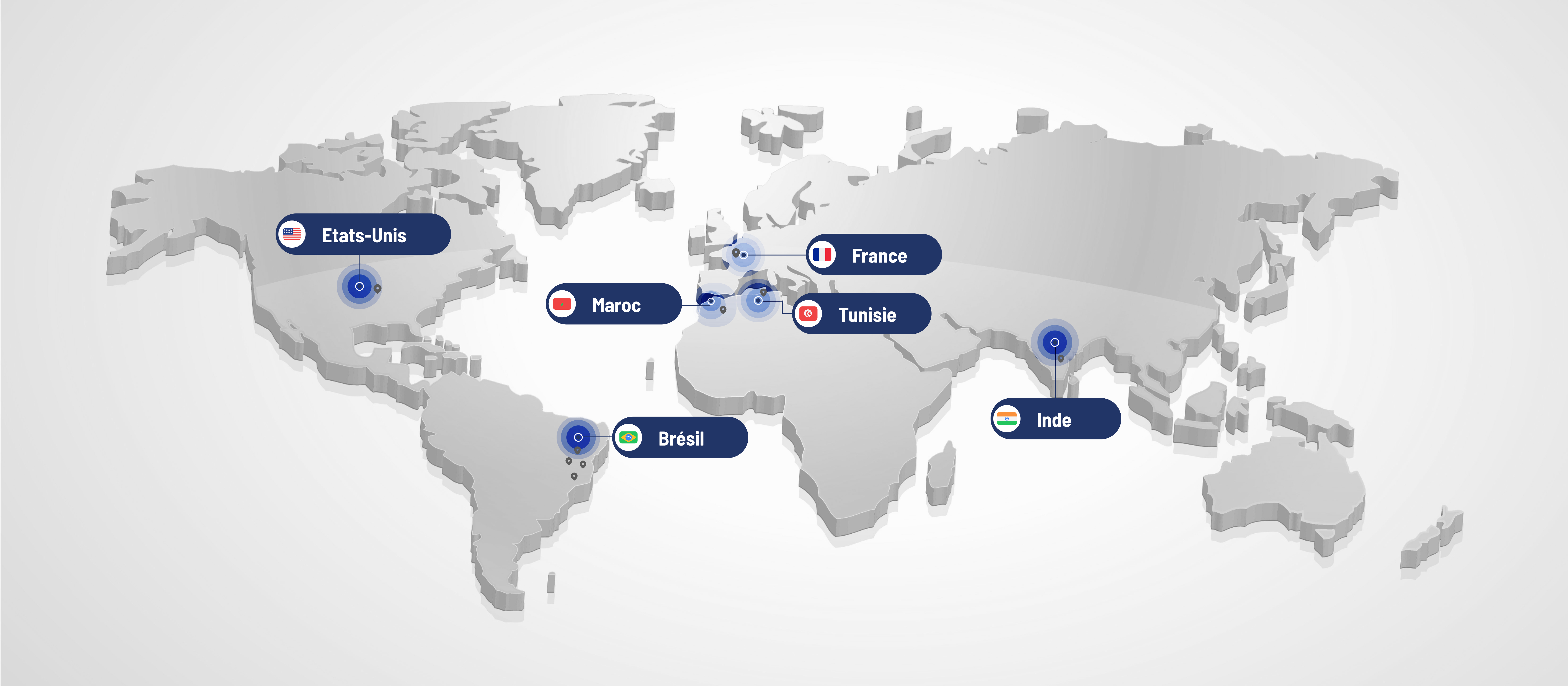